
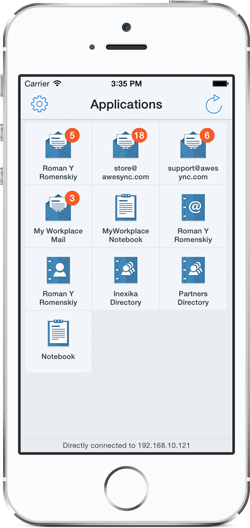
Maybe it is ironic that I am going to use the introductory words of C R Dooley, the then Director of TWI, from the Job Methods manual as my final words for this post. It is also noteworthy that “Less than 50% of the total time is usually consumed by the ‘DO’ part of the job.” Current thinking is that the true value added activities equate to less than 5% of a general process that is untouched by any improvement activities. The manual also identified these as the “greatest opportunities for improvement”. The Problem Solving Manual from TWI also identified “Make Ready” and “Put Away” as “movements of material without definite work accomplishment”. Taiichi Ohno wanted to add the importance of takt time, Standard WIP, flow, and pull style production to the idea of Kaizen. This was replaced by Shigeo Shingo’s P-courses that added the Industrial Engineering elements to process improvement activities. Surprisingly the first of the TWI programs that was dropped was the Job Methods program. Īs a side note, Toyota implemented the TWI programs in the early 1950’s. I encourage the reader to study the Job Methods manual to get a better grasp. This clearly shows that this is a continuous process. Additionally, I would also like to bring attention to “Use the new method until a better way is developed” statement. The following is a pocket card that was supplied as part of Job Methods program.Ī keen observer of the Job Methods can find the scientific approach of PDCA (Plan-Do-Check-Act) in it. The following is also part of Job Methods program.įigure 2: Steps 2 and 3 of Job Methods (TWI) The following figure is taken from the Problem Solving Manual from TWI. C R Dooley, the Director of TWI, stated the following “ TWI’s objectives were to help contractors to get out better war production faster, so that the war might be shortened, and to help industry to lower the cost of war materials.” There was a need to produce a lot in a short amount of time, and this required training operators to be better within a short amount of time. TWI was an emergency service by US to help nation’s war contractors and essential production. The reader should also be aware that the ECRS process and the questions have roots in USA’s Training Within Industry (TWI) movement that got started near the era that led to World War II. Please note that the steps are carried out in the order described above. Simplify: Is there any task that can be simplified to make the whole process faster and better? Does the operator spend a lot of time trying to sort things or fumble with things? Can we ultimately simplify all the steps?.Can we do the current step# 3 before Step# 1? Is there any logic to the current sequence of steps? Can we rearrange to create a better sequence. The Where, When and Who questions help us with this. Rearrange the Steps: Sometimes changing the sequence also allows us to take away waste from the process.Additionally, combining also reduces the number of discrete steps in the process. Combine the Steps: What are the steps that need to be done in series? Are there any steps that can be done in parallel? The Where, When and Who questions help us with combining steps to eliminate waste.The What and Why questions help us with this. Eliminate Unnecessary Tasks: The ultimate improvement is eliminating a task altogether.Going through these questions under the Description column and then following through the steps in the Countermeasure column is how one can improve a process. The right column is also known as the ECRS method.
#MYNOTES STEP 1 HOW TO#
This figure shows how to approach improving your process. The original title was “ Kaizen Teian Handobukku” which roughly translates to “ Kaizen through (Employee) Suggestions Handbook”. The following figure is taken from The Idea Book, edited by the Japan Human Relations Association (1980). Please note that the first step for Kaizen is to nurture your employees so that they become aware of problems. This post hopefully provides nuts and bolts on how to perform improvement activities. This post is about Kaizen and not Kaizen events.Ī lot of people talk about the need for doing Kaizen. Thus, there is a definite start and a stop to Kaizen Events, making this almost an oxymoron since Kaizen implies a continuous and never stopping state.

Kaizen just means incremental and continuous improvement towards the ideal state.Ī Kaizen Event on the other hand, means generally a week long team-based rapid improvement activity. There is a strong precedence in the lean community to call a “Kaizen Event” or “Kaizen Blitz” as “Kaizen”. Kaizen is most likely one of the most misused words in lean.
